“At Coriolis Composites, we are passionate about industry and innovation. We started from scratch 25 years ago! That’s why, today, we stand as strong relays of the French Fab* and the European industry as a whole. Thanks to our history, we embrace a culture of no limits: we have carried out ambitious projects despite all the difficulties, without ever failing. Today, we master a unique combination in composite materials: machine, software & expertise. This allows us to support our customers from the beginning of their project with defining their needs and designing of the part itself, all the way to the implementation and optimization of AFP machines.”
Clémentine Gallet, Coriolis Composites CEO, is also President of the SMEs group of the GIFAS with the goal to promote automation and the digital transformation of the factories. Clémentine is also sitting at the board of several industrial companies and competitiveness clusters.
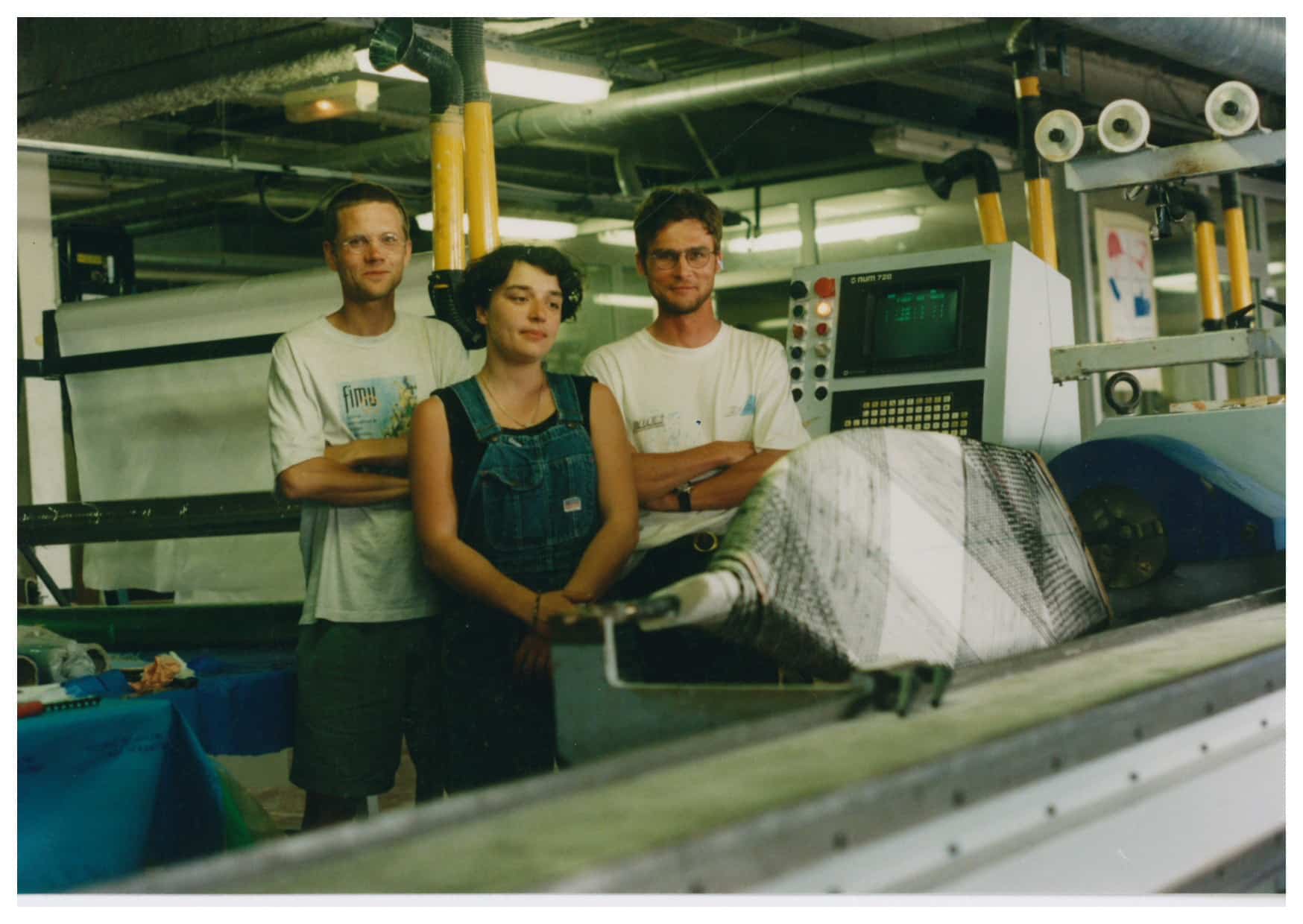
Born to innovate
The idea of Coriolis Composites was born in 1996, well before its founders, Clémentine Gallet and Alexandre Hamlyn, graduated from the engineering school.
MFTECH
MFTECH has become a global reference in robotics applied to filament winding..
Mission statement
A SPECIALIST IN THE IMPLEMENTATION OF COMPOSITE MATERIALS
Coriolis Composites develops, makes and markets robotic cells for fiber placement using a standard robot or gantry enabling the laying of continuous or discontinuous fibers, in all directions and on complex geometrical surfaces.
The aim is to enhance mechanical performance thanks to cost and energy efficient solution. We provide reliable technology to process a large variety of composite materials.
Coriolis Composites is a global expert in composite technologies, developing hardware and software solutions to enhance your production and design capabilities.
Choosing the reference in automated composite additive manufacturing means accessing:
Coriolis Composites is a global expert in composite technologies, developing hardware and software solutions to enhance your production and design capabilities.
Choosing the reference in automated composite additive manufacturing means accessing to:
WORLDWIDE LEADER
In robotic and gantry fiber placement cells and software
UNIQUE ROBOTIC TECHNOLOGY
Qualified on several flying programs
25 YEARS
Of experience in composite fiber placement including laser heating devices for dry fiber and thermoplastics
FULL SERVICE
Customer support in composite manufacturing
WORLDWIDE PRESENCE
With local support
SIXTY FAMILIES OF PATENTS
Extended in relevant countries (Europe, USA, Brazil, China, Japan, Korea…) and six trademarks registered in France and abroad